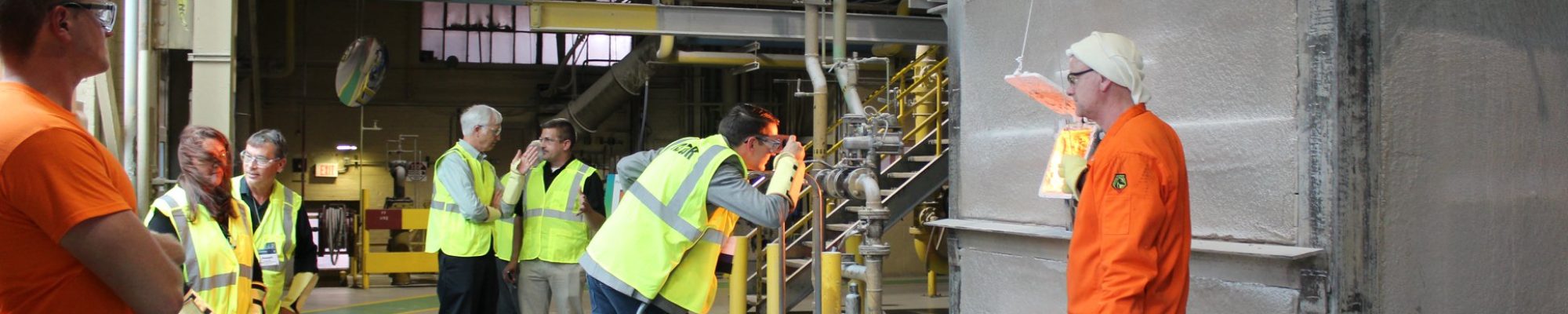
Furnace Rebuild
NSG Pilkington - Rossford, Ohio
Pilkington announced their plans to rebuild their 6F1 and 6F3 furnaces at the Rossford plant. The rebuilt furnaces manufacture flat glass to be used in building products such as decorative glass, low-e glass and self-cleaning glass, and in automotive glass (laminated and tempered).
IPS was responsible for the demolition of existing process piping and the installation of all new natural gas, oxygen, and nitrogen piping. In addition, our team installed cooling water lines, compressed air, combustion air piping and instrumentation of the 6F1 furnace. All installation work had to be performed while the demolition of the existing piping systems furnace was still operational to be Pilkington’s operational workflow needs.
Once the installation was complete, IPS moved down to the cold end of the furnace where the glass is cooled, cut, and prepared for shipping to self-perform the demolition and installation of all material handling equipment inclusive of power and control wiring. We installed new conveyors, glass cutters, clean room, and robotic equipment.
- 1,000,000 SF facility size
- Bid Build
- 6 months duration
- $3.5 million project value